Ghana’s construction industry faces a growing threat as the worldwide clinker shortage creates perfect conditions for counterfeit cement to infiltrate the market. For builders, contractors, and homeowners, this crisis represents more than just supply chain challenges—it potentially risks lives and investments.
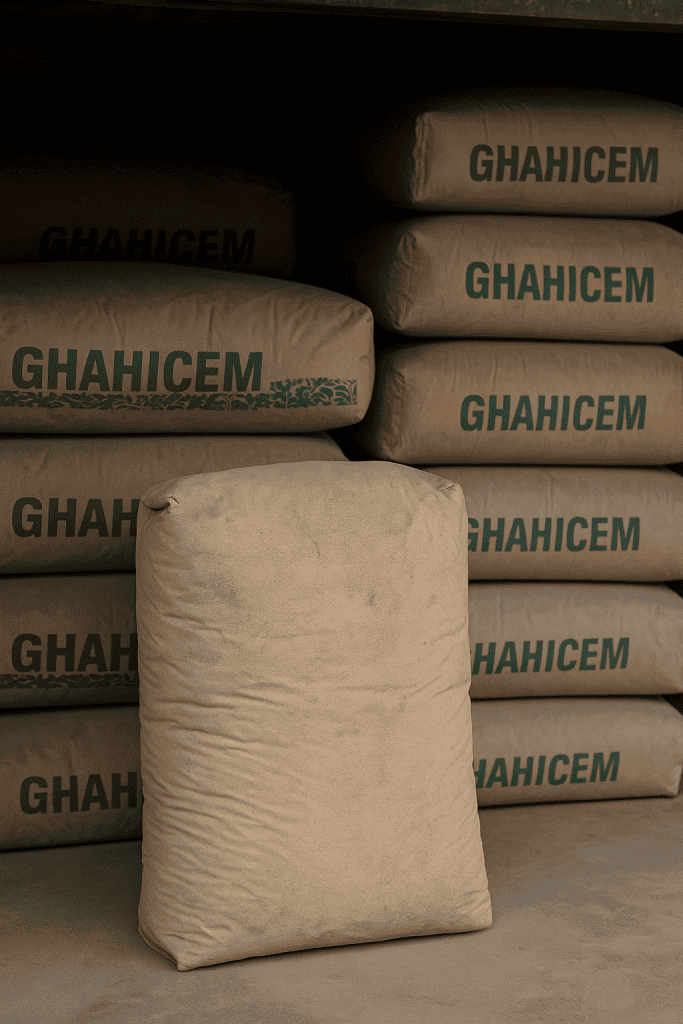
Understanding the Clinker Crisis
When you purchase a bag of cement, what gives it strength isn’t just the gray powder, but specifically the clinker content within it. Clinker serves as the essential active ingredient responsible for cement’s binding properties. During the curing process, it’s the clinker that triggers the chemical reactions necessary for hardening and durability. Without adequate clinker, you’re left with a substance that might look like cement but lacks the fundamental properties needed for structural integrity.
The current clinker shortage has created genuine cement scarcity throughout Ghana. Unfortunately, this situation has become fertile ground for unscrupulous suppliers selling substandard or entirely fake products to unwitting customers.
The Counterfeit Cement Landscape
Fake Cement Products
When confronted with shelves of seemingly identical cement bags, it can be challenging to identify counterfeit products. These fake versions typically contain minimal or no clinker, instead using fillers like sand, ash, limestone dust, or chalk. You might encounter them in unmarked bags, reused packaging, or even counterfeit branded bags.
Contrary to what you might expect, these fake products aren’t always budget-priced. Many scammers exploit the shortage by charging prices equal to or even higher than legitimate cement would normally cost, counting on buyers’ desperation amid perceived scarcity.
Perform a simple hardening test by mixing a small sample with water to create a thick paste. Genuine cement begins hardening within 30-60 minutes, generating noticeable heat during this process. Fake cement remains soft, doesn’t warm up, and might separate or remain powdery when dry. Also, inspect the packaging closely—legitimate products have consistent branding, batch numbers, and manufacturing details.
Advance Payment Schemes
When local suppliers claim they’re out of stock, you might encounter vendors who promise to deliver cement but require full payment upfront. These operators often work through temporary locations or exclusively by phone, claiming they can access limited supplies. After receiving payment, they either disappear entirely or continuously delay delivery with increasingly implausible excuses.
Research the vendor’s physical location and business history before transferring funds. Legitimate businesses will have established premises and verifiable references. Negotiate a split payment structure—a reasonable deposit followed by the balance upon delivery—request to inspect the actual inventory before making even partial payment, and insist on proper transaction documentation.
Compromised Building Materials
Sometimes the deception extends beyond the cement bag itself. Buildings constructed with fake cement develop serious structural problems surprisingly quickly. Concrete blocks crumble prematurely, mortar between bricks fails to bond properly, and foundations show defects within months rather than decades. These failures can lead to dangerous living conditions and financially devastating repairs.
Perform a basic strength test before using blocks or mortar made with suspect cement. Properly cured blocks should not allow your fingernail to scratch the surface. Properly set mortar should resist indentation. With larger projects, consider having material samples professionally tested—a small expense compared to rebuilding costs.
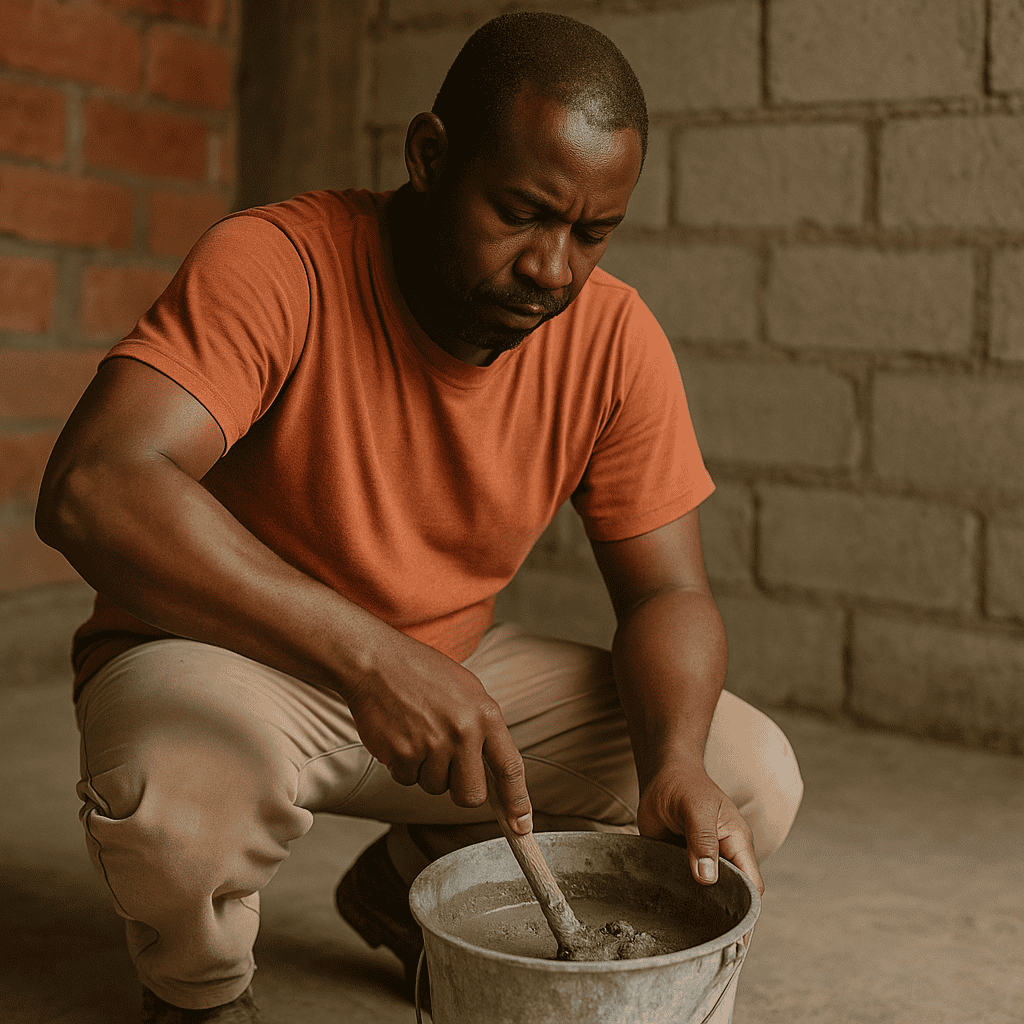
Misleading Marketing Tactics
You may encounter vendors selling what they claim is “special” cement with technical-sounding descriptions like “eco-cement,” “alternative cement,” or “next-generation blends.” These products frequently lack legitimate certification or standardization documentation. When questioned about clinker content or manufacturing processes, sellers typically provide vague responses or change the subject.
Request specific documentation showing adherence to Ghana Standards Authority requirements. Legitimate cement manufacturers provide detailed specification sheets and certifications. Be suspicious of unusual terminology not common in the industry. Ask direct questions about clinker content—reputable sellers can answer these queries with confidence and precision.
The Deceptive Pricing Strategy
Understanding the economics of this counterfeit market helps protect you from becoming a victim. Despite being significantly cheaper to produce, fake cement products are rarely sold at bargain prices. Instead, scammers employ sophisticated pricing strategies:
They often price counterfeit products at or slightly above market rates, creating the illusion of legitimacy through premium pricing. They capitalize on buyers’ desperation by exploiting the clinker shortage to create artificial scarcity. Many purchasers willingly pay inflated prices, believing they’ve secured scarce genuine cement. The higher price point creates a false impression of quality when, in reality, production costs are dramatically lower for counterfeiters, generating enormous profit margins at consumers’ expense.
Protecting Your Construction Investment
Safeguarding your building project requires both vigilance and knowledge. Source cement only from established, reputable suppliers with permanent locations and verifiable business histories. Before making major purchases, request and test samples using the abovementioned methods. When possible, visit physical locations to verify inventory before transferring funds.
Quality verification extends beyond the initial purchase. Legitimate cement produces noticeable heat as it cures during construction. Properly hardened cement should resist scratching and maintain consistent color and texture throughout. If you notice unusual variations or behaviors during mixing and application, stop using the product immediately and have it tested.
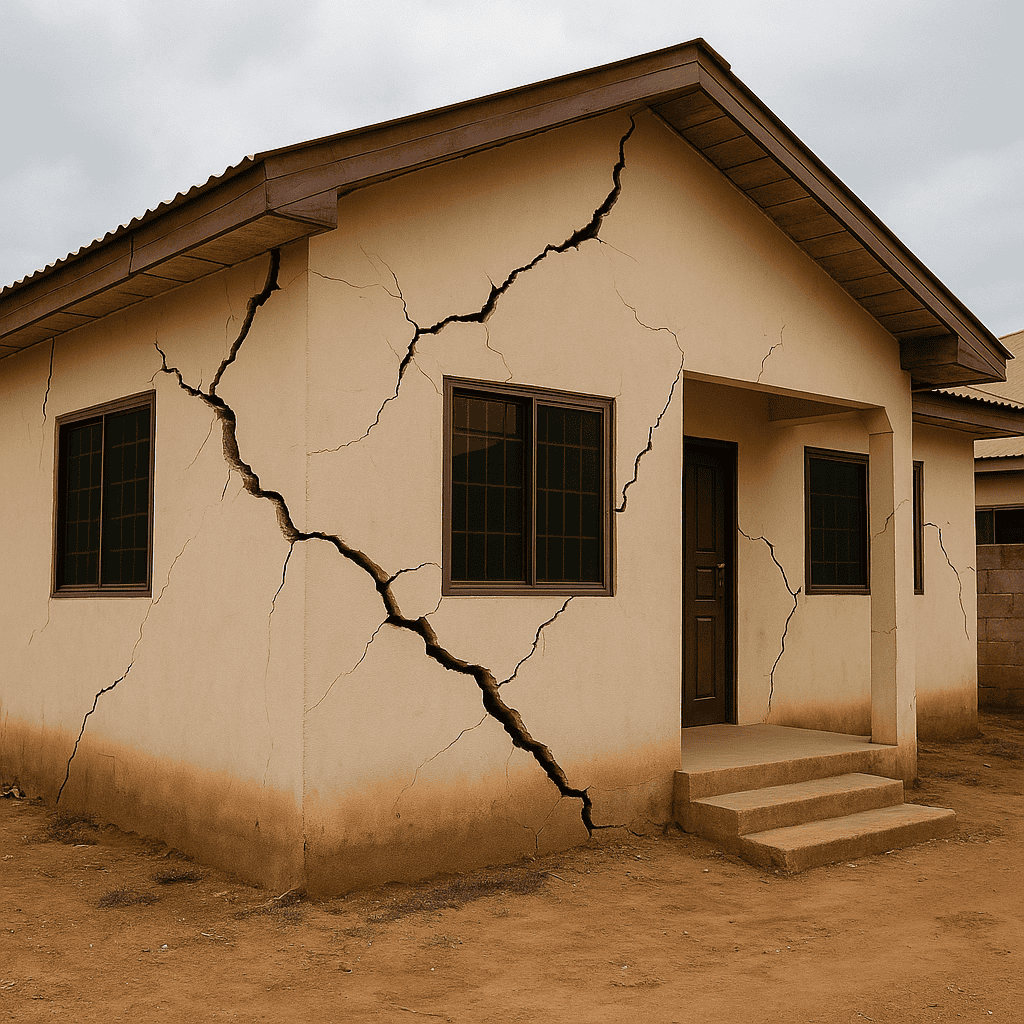
The High Cost of Cutting Corners
Using fake cement creates dangers extending far beyond initial construction challenges. Structural failures can lead to catastrophic building collapses that threaten lives. Even when buildings remain standing, they often require expensive reinforcement as defects emerge. The building’s lifespan dramatically shortens, creating an ongoing financial burden of escalating maintenance costs. For contractors, there’s potential legal liability for using substandard materials, even unknowingly.
This common story of builders using substandard cement clearly illustrates these dangers. After investing in building a small apartment complex, it is discovered that the cement they purchased contained virtually no clinker. Six months after completion, walls begin cracking and floors sagging. The entire structure required extensive reinforcement, costing nearly as much as the original construction. What seemed like a fortunate find during the shortage became a devastating financial setback.
Community Defense Against Counterfeit Products
Ghana’s construction community must work collectively to address this threat. Consider forming purchasing groups to leverage buying power with legitimate suppliers. When you encounter suspicious cement products, document and report them to the Ghana Standards Authority. By sharing information about verified suppliers and known counterfeiters, you protect not just your own projects but the broader construction ecosystem.
Education remains a powerful defense—ensure construction workers understand visual and physical indicators of fake cement. For larger projects, third-party quality testing costs represent minimal expense compared to potential reconstruction costs.
Building a Secure Future
The temporary inconvenience of delayed construction while sourcing legitimate materials pales in comparison to the devastating consequences of building with counterfeit products. Proper construction materials represent an investment in safety, durability, and long-term peace of mind.
By remaining vigilant and applying the verification techniques outlined in this article, you can protect your building projects from this growing threat. Your decisions today about cement quality will determine whether your structure stands strong for generations or becomes a cautionary tale about the dangers of counterfeit building materials. This information could save lives and livelihoods throughout Ghana—share it widely with others in your community who might be vulnerable to these scams.